Galeria Kaufhof
GALERIA Kaufhof optimises print performance with output management from AKI
The customer
GALERIA Kaufhof GmbH, based in Cologne, is one of Europe’s leading department stores’ companies. With its innovative and successful concept, the company presents modern shopping and experience worlds. GALERIA Kaufhof GmbH currently operates 103 department stores and 16 sporting goods shops in Germany and 16 department stores in Belgium. The company has approx. 21,500 employees.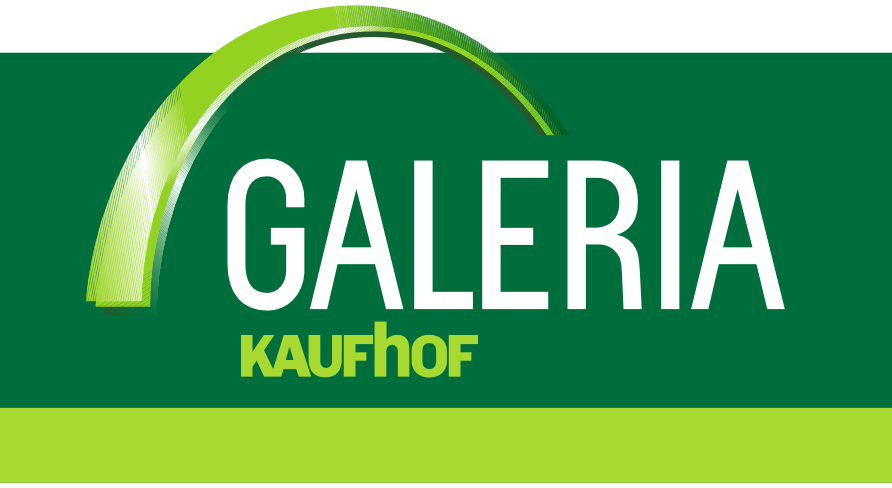
- Sector Trade
- Task Stabilise the printing processes, highest failure safety, further use of the existing printing stencils
- Top-Challenge Optimum print performance even at highest load peaks
- Solution AKI PrinTaurus GUI, UniSpool
- Top benefits Simple, central administration of the large, heterogeneous printer landscape, no downtime by AKI experts
The task
GALERIA Kaufhof uses approximately 1,000 printers in six warehouses. As a multi-channel department stores’ with an extensive online offering, large quantities of printouts are generated every day. “We create around 100,000 to 130,000 print jobs per day at our warehouse locations,” explains Marcus Weiss, Head of Procurement and Logistics Systems at GALERIA Kaufhof. “In seasonal business, such as Christmas, this number can multiply.” All the receipts needed for warehouse operations in the operative business are printed – numerous consignments of goods are sent to our customers at high frequency at each packing station – and we control several packing stations at each warehouse location. Of course, we can’t let the printers throw a spanner in the works.” GALERIA Kaufhof’s six distribution centres use standard printers from various manufacturers; the common requirement for all models is double-sided printing. The printers are controlled by the warehouse management system or by various terminals. Approximately 5,000 different print variants – print templates – which map the actual print logic upstream, generate all relevant information for the print output. However, the previous output management solution repeatedly had performance problems, and there were even sporadic failures, for example during the above-average demand in the Christmas business. During such disruptions, the entire spooling system had to be restarted by the provider – resulting in a packet jam. Because during this time, no printer could be controlled. In addition, GALERIA Kaufhof lacked a simple way to administer individual printers without paralysing the entire printing system.The solution
“Our printer landscape must function properly,” explains Weiss. “Even if the failures were sporadic; we didn’t want to tolerate such waiting times any more.” Therefore, the decision was made to purchase a new output management system. The basic requirements for the selection were operability under AIX and integrability into the existing GALERIA Kaufhof warehouse management system. In addition, the new spooling system should run very stable and guarantee the highest printing performance. “Because of our e‑shop, one hundred per cent availability of the print manager must be given,” says Weiss. A very fast printing speed of the delivery papers was also one of the priorities. In addition, it had to be possible to detect faults quickly and, above all, to rectify them quickly – without having to reboot the entire system. At best, the new solution should cause little to no change for the users in the individual locations. Another core requirement: the fully automatic backup of the printing stencils – on a daily basis. In addition, competent, easily accessible support with problem-solving competence was desired. “This may sound banal, but unfortunately it is often lacking,” Weiss explains. GALERIA Kaufhof took a close look at various providers. Finally, the IT departments ‘System Architecture’, ‘Procurement and Logistics Systems’ as well as ‘Supply Chain Management Logistics’ decided in favour of AKI’s intelligent output management solution. “The solution offer, which was exactly tailored to the problem situation, convinced us, so we wanted to test the software intensively”, says Weiss. The offer and project phase took place step by step with clearly defined milestones. After the solution designed by AKI had been extensively tested on a productive server in accordance with the catalogue of requirements and had easily passed the final live tests, there was nothing standing in the way of purchasing the software. The software is modular in design and ensures high-performance, economical and convenient printing even in heterogeneous printer landscapes of all sizes. The solution was quickly implemented and there was an on-site introduction in the pilot warehouse as well as joint training for all users of the individual warehouses after the pilot. “The system introduction went without a hitch and even special requirements such as controlling individual paper trays of a printer via print template run perfectly with a specially developed AKI script”, remembers Klaus Kullick, Team Leader Logistics Systems at GALERIA Kaufhof. “We are very satisfied with the performance of the system. So far we haven’t had a single failure. Printing is now really always possible and no faulty print job blocks the entire system,” explains Weiss. In addition, the AKI solution brings transparency to the entire print path – from the print job, to print queues, to the final printout, the status of all print jobs can be tracked in the system – no print job is lost any more. “And via the graphical user interface, users can also redirect several print jobs to other printers at the same time, if necessary, in the event of a malfunction. Our users on site describe this additional function as the ‘non plus ultra’,” Weiss is extremely satisfied. “We have great confidence in the output management solution, but also in AKI as a company – because the support that the company provides has convinced us all along the line.” Klaus Kullick adds: “We recently had a request for support, which was answered promptly and completely satisfactorily.” “The simple and straightforward operation saves a lot of hassle compared to the print manager that was in use before,” explains Weiss. The area manager sums up: “The system has no problems whatsoever even under heavy load, and that is the decisive measure for us. Especially in retail, there are of course load peaks, and even at Christmas the system ran absolutely stable. As it is in IT, the best system is the one you don’t hear about. And I don’t hear anything from AKI – that’s great.”“The system has no problems whatsoever even under high load, and that is the decisive parameter for us. Because especially in retail, there are of course load peaks, and even in the Christmas business, the system ran absolutely stable.”
The benefits
- Highest print performance and reliability
- Easy management
- Single point of control – central administration of the printer network with intuitive graphical interface
- Quick, straightforward drag-and-drop intervention for printing problems
- Saving costs, time and nerves
AKI PrinTaurus GUI
- Single Point of Control
- Intuitive interface for managing print servers, queues and ports
- Vendor-independent, simple configuration of many printers/queues, ports etc.
UniSpool
- Spooling system for AIX
- Strong performance
- High reliability
- Interface for further use of existing print templates
Kontakt
Sagen Sie uns, ob wir Sie unterstützen können. Nehmen Sie mit uns Kontakt auf. Unverbindlich und jederzeit.